What is Porosity in Welding: Best Practices for Preventing Permeable Welds
What is Porosity in Welding: Best Practices for Preventing Permeable Welds
Blog Article
Porosity in Welding: Identifying Common Issues and Implementing Best Practices for Avoidance
Porosity in welding is a prevalent issue that usually goes unnoticed till it triggers substantial problems with the honesty of welds. In this discussion, we will discover the vital factors adding to porosity development, examine its destructive effects on weld efficiency, and review the finest techniques that can be adopted to reduce porosity occurrence in welding procedures.
Common Reasons For Porosity
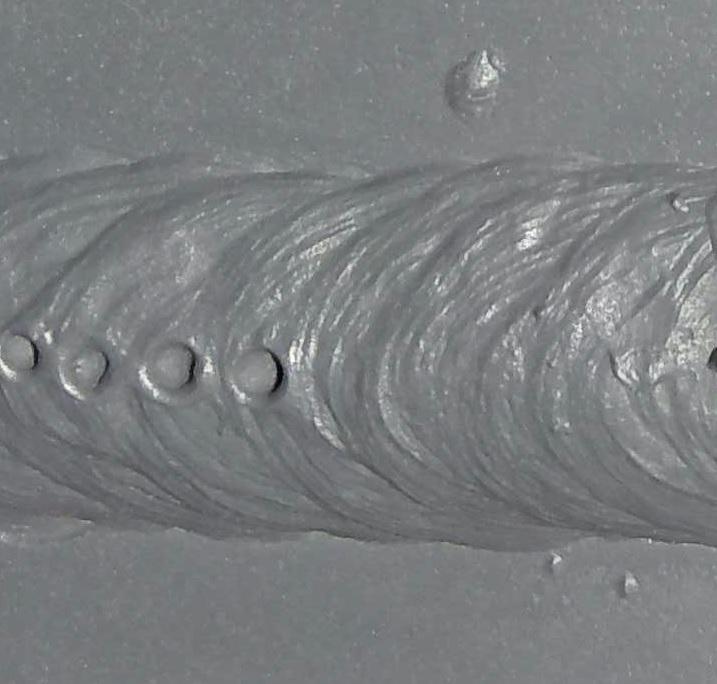
One more regular culprit behind porosity is the existence of impurities on the surface of the base metal, such as oil, oil, or corrosion. When these pollutants are not properly gotten rid of prior to welding, they can evaporate and come to be entraped in the weld, triggering flaws. Furthermore, utilizing filthy or damp filler products can introduce impurities right into the weld, adding to porosity issues. To mitigate these usual sources of porosity, detailed cleaning of base metals, correct securing gas selection, and adherence to ideal welding criteria are important techniques in accomplishing premium, porosity-free welds.
Effect of Porosity on Weld High Quality

The existence of porosity in welding can substantially compromise the architectural stability and mechanical homes of welded joints. Porosity develops gaps within the weld steel, weakening its general stamina and load-bearing ability. These spaces serve as tension focus factors, making the weld more susceptible to splitting and failure under applied loads. Additionally, porosity can reduce the weld's resistance to corrosion and various other environmental variables, better lessening its long life and efficiency.
One of the key repercussions of porosity is a decline in the weld's ductility and toughness. Welds with read the full info here high porosity degrees often tend to exhibit reduced effect stamina and reduced capacity to deform plastically before fracturing. This can be especially worrying in applications where the welded parts are subjected to dynamic or cyclic loading problems. Furthermore, porosity can restrain the weld's capability to properly transmit forces, resulting in early weld failure and possible safety and security threats in crucial structures.
Finest Practices for Porosity Avoidance
To enhance the structural integrity and high quality of bonded joints, what details steps can be executed to minimize the event of porosity during the welding procedure? Utilizing the correct welding strategy for the certain product being bonded, such as readjusting the welding angle and gun setting, can better stop porosity. Routine evaluation of welds and instant remediation of any kind of issues identified throughout the welding procedure are vital methods to avoid porosity and produce top notch welds.
Importance of Proper Welding Techniques
Applying appropriate welding strategies is critical in guaranteeing the structural stability and top quality of bonded joints, developing upon the foundation of reliable porosity prevention steps. address Extreme warmth can lead to boosted porosity due to the entrapment of gases in the weld swimming pool. Furthermore, making use of the suitable welding parameters, such as voltage, current, and travel rate, is critical for attaining audio welds with marginal porosity.
Furthermore, the selection of welding process, whether it be MIG, TIG, or stick welding, should align with the details needs of the task to make certain optimum results. Proper cleaning and prep work of the base metal, as well as choosing the right filler material, are likewise important elements of skillful welding methods. By sticking to these best techniques, welders can decrease the danger of porosity development and generate high-grade, structurally sound welds.
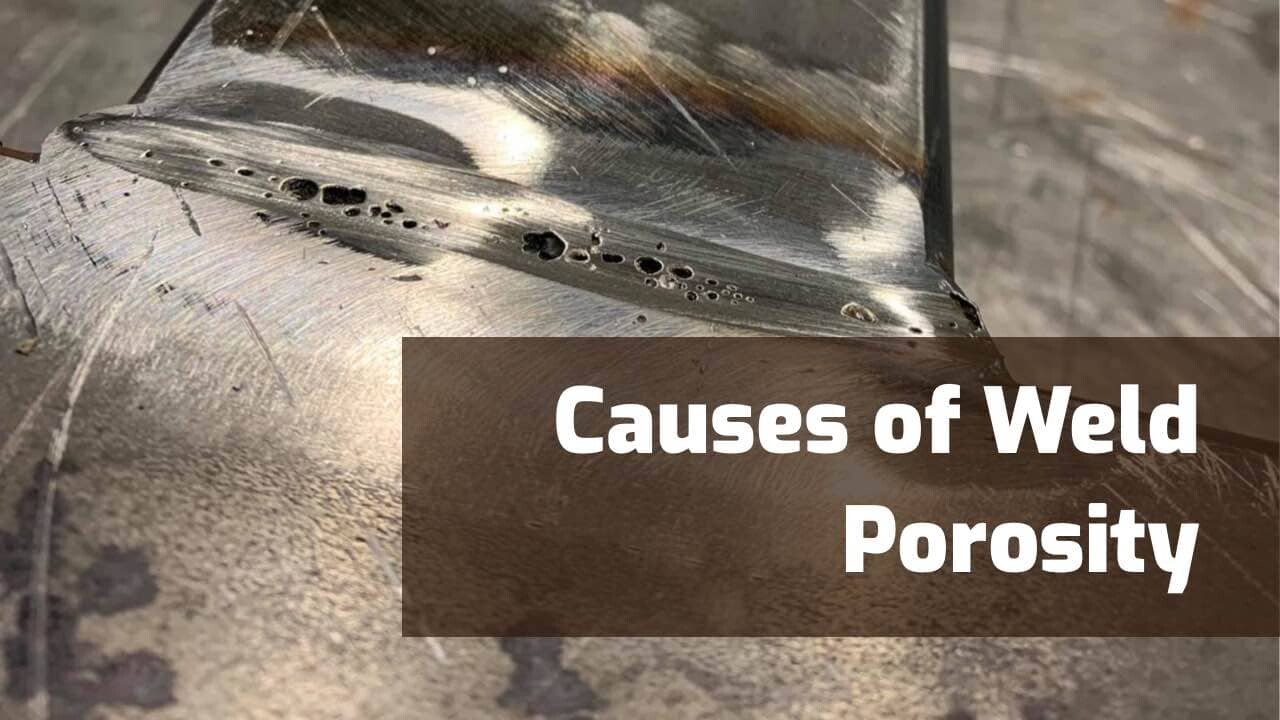
Checking and Quality Assurance Steps
Quality control steps play an essential role in validating the stability and integrity of welded joints. Testing procedures are vital to detect and avoid porosity in welding, making certain the stamina and sturdiness of the final item. Non-destructive screening approaches such as ultrasonic screening, radiographic testing, and visual inspection are typically used to determine possible flaws like porosity. These methods permit the evaluation of weld quality without endangering the stability of the joint. What is Porosity.
Post-weld examinations, on the various other hand, assess the last weld for any problems, consisting of porosity, and verify that it satisfies defined standards. Applying view website a thorough top quality control strategy that consists of complete screening procedures and evaluations is extremely important to reducing porosity concerns and guaranteeing the total high quality of welded joints.
Conclusion
To conclude, porosity in welding can be an usual issue that influences the top quality of welds. By recognizing the typical sources of porosity and executing best practices for avoidance, such as proper welding methods and screening steps, welders can make sure high top quality and trustworthy welds. It is important to focus on prevention methods to lessen the occurrence of porosity and keep the stability of bonded frameworks.
Report this page